Advantages of liquid silicone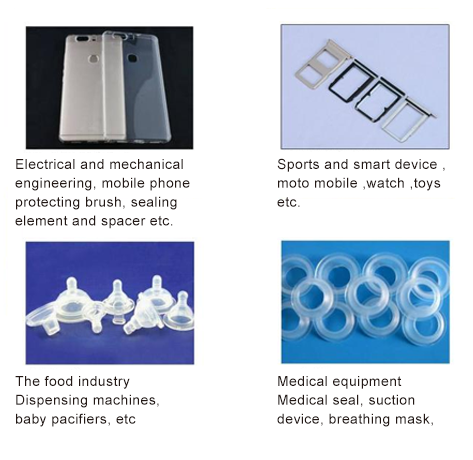
application
1. Non-toxic to human body, safe and sanitary, odorless and tasteless;
2. Good transparency and can be disinfected;
3. No pollution to the environment and be degradable
performance
1. Good tactility, elasticity and aging resistance;
2. Good resistance to high temperature properties, thermal stability (continuous working temperature
can up to 180 ° C).
3. Excellent low temperature performance (-50 ° C still with softness);
4 excellent electrical insulation, when burning no harmful substances will be produced.
Electrical and mechanical engineering, mobile phone protecting brush, sealing element and spacer etc.
Sports and smart device , moto mobile ,watch ,toys etc.
》Properties of liquid silicone
Characteristics difference between liquid silicone molding and ordinary injection molding products:
1) liquid silicone is a kind of thermosetting material;
2) rheological behavior: low viscosity, rapid curing, shear thinning, high thermal expansion coefficient;
3) good fluidity, low requirements for mold locking force and injection pressure, but high requirements
for injection accuracy;
4) exhaust design is relatively difficult. Some products need to be designed with sealed and vacuum-
pumped structure, which requires high precision of the mold.
5) design the cooling structure of the cylinder and the casting system, and design the heating system
of the mold.
》Design essentials of liquid silicone mold heating
Mould temperature control.
Liquid silicone injection mold under the mold temperature 120 ~ 150 ℃ cause the curing reaction,the key point is to control mold temperature
1) the mold surface temperature shall be stable.
If the surface temperature is too high, which will produce products burning, parting line cracking, brittle products and other phenomena.
If the surface temperature is too low and the glue curing speed is slow which will cause the product can not demoulding and other quality problems;
2) the temperature of the mold shall be heated evenly.
Mould heating is not uniform, the temperature difference is large,which will make the plastic flow not stable, easy to appear air, injection dissatisfaction and other phenomena;
3) position the heater
Sufficient distance should be kept between the heater and the parting line to prevent the formwork from warping and deforming, leading to the formation of flash edges of finished products;
》Comparison of mold temperature control heating mode:

》Comparison of mold temperature control heating mode:
Key points of pouring design of liquid silicone mold
Runner pouring system design.
Cold runner molding is one of the important processing characteristics of liquid silicone rubber
1) cooling system shall be designed inside the cooling nozzle:
There is a big difference between cold runner molding and hot runner system. Water line should be designed inside the cold nozzle, and an effective heat insulation layer should be set between the mold cavity and cold runner to isolate temperature transfer.
If the sub-runner is too hot, the material will begin to solidify before injection, and the product is prone to cracking and no injection products will be produced.
2) the cooling nozzles shall be designed with a closed system for automatic production with a shorter cycle:
Cold nozzle design needs to use valve gate closed system, the gate design is between 0.5-0.8mm, the valve system needs to design a highly adjustable structure, which is easily to fine tune the flow through the valve.
3) the cold nozzle needs to be designed with the injection amount control system
When injection molding silicone seals of micro products, and the product weight is less than 1 g, the amount of precision control system need to be designed to ensure that the amount of plastic flow can be controlled and be adjustable.
》For micro products,the amount of precision control system need to be designed to ensure that the amount of plastic flow can be controlled and be adjustable.
Application of liquid silicone in waterproof mobile phone
The innovative application of liquid silicone in waterproof structural parts of mobile phones solves the problem of water damage of mobile phones. The injection molding methods of metal + silica gel, plastic + silica gel, glass + silica gel and other secondary forms will become the new trend of mobile phone waterproof.
》Advantages of two-color silicone injection molding waterproof over traditional mobile phone waterproof:
Traditional mobile phone waterproof adopts coating adhesion , ultrasonic welding, due to the need for manual operation in the middle, its assembly accuracy, stability can not be guaranteed, which means easily damaged and the waterproof effect is poor.
The waterproof structure of liquid silicone injection molding is simplified, the overall structure is compact, the assembly precision and repeat precision are high, the waterproof effect is improved, and the waterproof grade is above grade 5.
The secondary molding bond strength is high of liquid silicone injection molding and metal, plastic and other materials , which can be repeatedly disassembled and easy to be replaced and waterproof stability.
》Comparison of mobile phone soft rubber jacket -- TPU and liquid silicone
silicone jacket
Advantages: non-toxic to human body, good buffering performance, high wear resistance, oil resistance, water resistance, good flexibility, comprehensive protection, and it will not turn yellow.
It can be used in double color gluing mould to make waterproof sheath.
Disadvantages: slightly poor fitting with the fuselage
TPU jacket
Advantages: high wear resistance, high strength, outstanding cold resistance, oil resistance, water resistance, mycete resistance, good flexibility
Deficiency: easy to deform and turn yellow
Zhenxiong provides customers with integrated solutions
For the silicone mold, zhenxiong provides more professional, more convenient solutions.
Zhenxiong can provide solutions according to customer requirements, including:
Front mold cold nozzle and front mold structure design
According to the hot -half structure to provide cold nozzle whole delivery (cold nozzles, front board and insulation board are delivered to the customer after zhenxiong processes and assembles them)
Provide installation technical guidance and trial mold technical services.